Low-noise chillers for data centers: Peace and quiet for your cooling needs
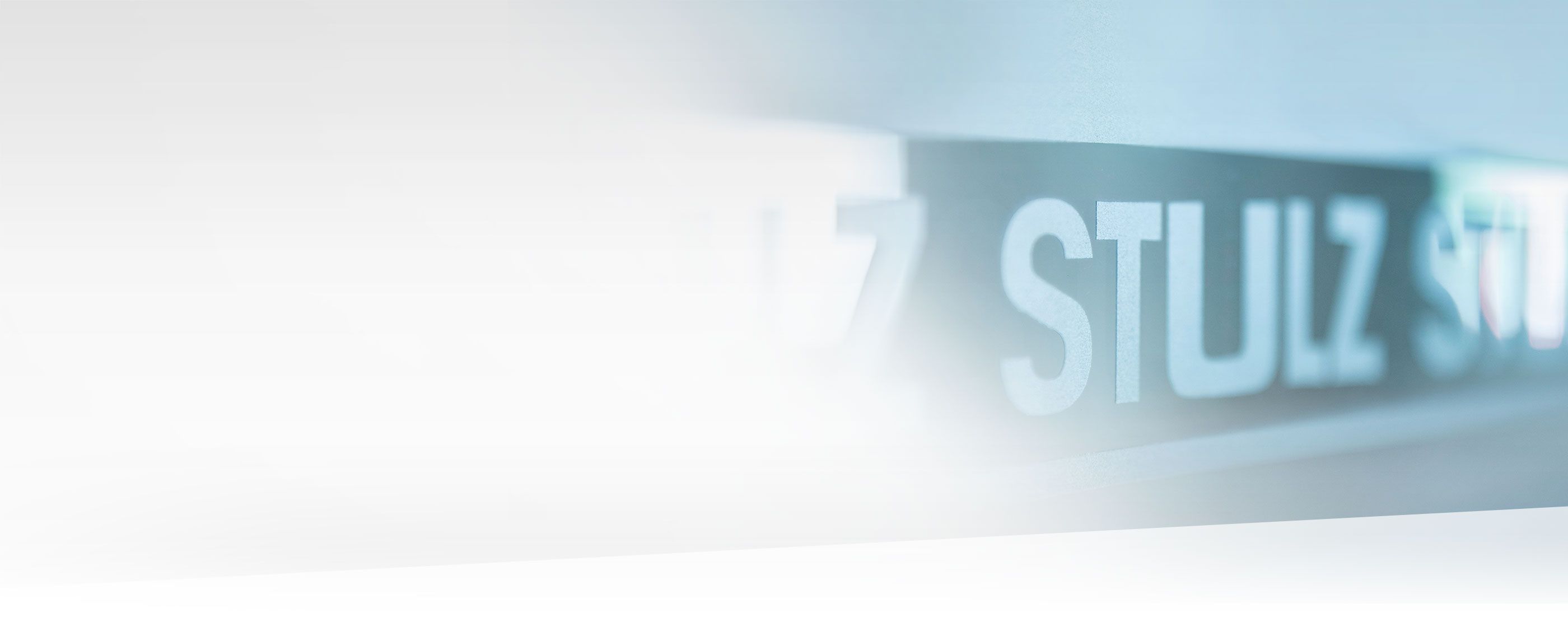
For data centers close to residential areas, compliance with noise regulations is extremely important. Air conditioning systems can be problematic in this respect. Chillers with a cooling capacity of 500kW, in particular, often generate a lot of noise during operation. Here, low-noise solutions from STULZ ensure the necessary noise reduction.
As long as data centers are predominantly located on so-called greenfield sites outside of urban centers, noise emissions are not a major issue. However, these days even large data centers are being built ever closer to populated districts, so that data center operators can no longer avoid tackling the subject of noise optimization. This is especially the case in Germany, where strict noise regulations must be met, particularly in the hours of evening and night. Industrial and service companies – not to mention operators of concert halls and sports facilities – could tell us a thing or two about conflicts with local residents who say they are disturbed by noise. For a data center running in continuous operation 24/7 all year round, there is genuine cause for concern.
Avoiding critical thresholds from the start
To prevent potential conflict long before it rears its ugly head, data center operators must consistently use solutions with noise emissions that do not come anywhere near critical thresholds. Of course, this also applies to cooling systems with compressors, pumps and fans that can produce not inconsiderable noise. Here, we recommend only installing systems and components that are so quiet that their operation is unproblematic, even at night time. However, what sounds good in theory is not always simple to achieve in practice. A classic dilemma is posed by chillers, which exceed approx. 500 kW of cooling capacity and are situated on or next to a data center. The lowest noise emissions would be achieved using soundproof encapsulated compressors and maximum size fans, which produce the necessary airflow with comparatively low speeds and can also keep noise to a minimum – as a system. However, it is evidently not easy to reconcile soundproof encapsulated compressors and large fans with the standardized sizes of chillers. Hence the restrictions on length and width imposed by chillers mean that smaller fans are generally installed. These deliver the necessary capacity, but only at the price of higher speeds, which increases both noise emissions and energy costs.
The rise in heat loads that goes hand in hand with the increased heat density in today's data centers has made the problem even worse: in order to overcome the resulting amounts of heat quietly and efficiently, even more chillers would in fact need to be installed on numerous data center sites. Sometimes, however, there is insufficient space for this, so that the existing CW systems are under even more load than they were already. The result is higher electricity costs and high noise emission.
To provide data center operators with a way out of this dilemma and enable chillers to be used in residential areas, too, quite a number of manufacturers are equipping their fans with noise-reducing diffusors. Hamburg-based precision air conditioning specialist STULZ, on the other hand, is taking an alternative route, and manufactures its Cyber Cool 2 chillers with a view to reduced noise levels right from the start. Even during the development phase, thorough research has gone into compressors, fans and pumps, to examine their noise emissions during operation. Based on the results of these tests, systematic measures have been taken to minimize the amount of noise generated.
Soundproof encapsulated compressors, maximum size fans
The first approach to tackle noise reduction involved the compressors. In some chillers, they are so exposed that their operating noise is diffused into the environment largely unfiltered. Compressor housings, too, are frequently not noise optimized and, depending on their design, can even increase the noise level. At STULZ, on the other hand, the compressors are housed in a special, soundproof encapsulated chamber. Like the walls of a recording studio, their interior walls are completely lined with sound-insulating material, so that as little noise as possible reaches the outside. This first step in itself has greatly reduced noise emissions.
While the development of a soundproof encapsulated compressor chamber was a solution that enjoyed the benefit of experience from other industries, the question of optimizing fan noise levels was considerably more complex. Here, we needed to design a compact construction that enabled noise and efficiency values to be optimized while adhering to the chillers' standard surface dimensions. STULZ solved this difficult task by installing maximum size fans. These make the best possible use of the available space, and are lined up next to one another so closely that you can barely slip a proverbial sheet of paper between them. And finally, with diameters of 910 millimeters, they are so large that they can move the necessary volumes of air removed at moderate speeds, thereby working quietly and energy efficiently. In order for the strengths of this new fan system to be exploited to the full, the entire air conduction system, from the intake through the heat exchangers to the fans, had to be redesigned.
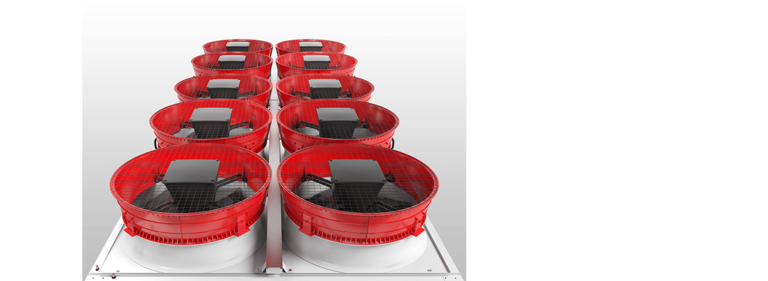
The maximum size fans of the STULZ CyberCool 2 - here with top-mounted diffusors - exploit the available surface to the full
Free Cooling coil with large surface area as another vital factor
STULZ's noise optimization concept is not just limited to soundproof compressor chambers and maximum size fans with new air conduction, however. Free Cooling coils with a large surface area, which have been technically optimized based on sophisticated CFD analyses, are also important when it comes to reducing noise emissions. Here, STULZ's aim was to ensure that the coil surface was exploited to the full, as Free Cooling only reaches its maximum effectiveness if this prerequisite is met. If this objective is achieved, there is both a lack of air turbulence and therefore reduce noise. The answer to this problem was special air baffles, which ensure an optimum flow of air onto the internal coil elements. Free Cooling coils that have been flow-optimized in this way enable the system to switch to Mixed mode – combined Free Cooling and compressor cooling – or even pure Free Cooling mode, if the outside temperature permits, as soon as possible. This keeps the overall running time of the compressors low and thereby noticeably reduces noise emissions produced during their operation. Furthermore, the optimized air conduction lowers the fan speed, therefore also contributing to reduced operating noise and energy costs. Incidentally, the CW system also benefits from the large coil surfaces in DX mode, as they ensure low condensing temperatures and a lower airflow speed.
Conclusion
With chillers like the STULZ Cyber Cool 2, data center operators now have solutions to hand for effectively reducing the noise emissions of the air conditioning system – with improved energy efficiency as a positive side effect. A prerequisite for the optimum function of this and similar solutions is, of course, that the entire refrigeration system is regarded and analyzed as a single unit, and the various steps towards optimization are taken progressively. If the above is complied with, the solution may be of interest in other areas, not just in data centers. The STULZ concept has now extended beyond the data center sector to draw attention from different fields of industry, and has thus acquired the status of a true cross-industry innovation.
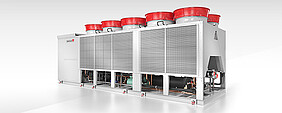